Danit Peleg talk @ TIPE Virtual conference on January 28th, 2021 | 7:00 PM CET
Join us and Danit Peleg at TIPE 3D Printing Virtual conference to find out more about 3D Printing Fashion Industry and 3D-CPAM experiment inside Cloudi Facturing project.
Register at: https://www.tipe3dprinting.com
ABOUT THE CONFERENCE
TIPE 3D Printing | 2021 Technology. Industry. People. Economics. Youth
With a focus on case studies, additive manufacturing user applications, visionary talks on the future, and people shaping the industry, TIPE | 2021 curates an inspirational all-female agenda of speakers and panelists. Long-lasting connections and networking opportunities are emphasized throughout this human-centered event, which welcomes all members of the additive manufacturing and related community.
UPDATE: Successful first 3D print test with two heads
As a result of ten months work on 3D-CPAM experiment, the robust modular machine – Modax3D printer – that enables the production of tough, accurate, and complex industrial parts using both FDM/FFF 3D printing technology and CNC milling on the same machine simultaneously developed by Mikrotvornica, was upgraded by adding another print head. Read more..
Armis Slide: 3D Printed Shoes Made in a Single Print
3D printing has had an revolutionary impact on the industrial world at numerous levels. While in some areas, researchers are producing groundbreaking studies and inventions as in medicine, other innovators are focused on improving essential needs, like clothing and shoes. That doesn’t mean, however, that they aren’t having fun in doing so. The latest in 3D printed footwear has just been released by Yanko Design, featuring some pretty cool (and comfortable looking) designs that they claim to 3D print in one hour.
The Armis Slide, classic and elegant in design, features a simple structure by Shun Ping Pek—and so much so that the whole shoe can be 3D printed at once. Consisting of an inner mesh and an outer covering designed to protect the foot with several different parts, the shoe is shock-absorbing and can be soft in one area while more rigid in another—as the wearer wishes, based on customization via data from foot pressure graphs.
The inner mesh is the result of a generative design algorithm, also responsible for preparing the entire structure of the shoe, including the placement of the outer shell. For this model, Shun Ping Pek relied on resin-based 3D printing. While the Armis Slide may not appear extraordinarily sturdy, hopefully (we have not been supplied with a price point thus far) the greatest benefits in additive manufacturing play a role through affordability, along with incredible speed in manufacturing, and the ability to make modifications for customer-specific comfort.
Apparel and footwear designers run the gamut enjoying 3D printing these days. Digital fabrication is a tool obviously in step with the artistic spirit as the middleman and factories can be cut out altogether. A designer can come up with an idea at any time of day or night, convert it into 3D, and begin printing prototypes or actual functional pieces (depending on their level of software, hardware, and material) in small batches.
From some pretty crazy looking interpretations of the high heel from artist/designers like Francis Bitonti and Annie Foo—to basic DIY shoes focusing on customization and available on platforms like Thingiverse—the ongoing evolution has been apparent. This is well-marked also by the emergence of multiple footwear leaders like Nike, New Balance, Adidas, Under Armour, Reebok and more. For instance, Adidas launched the 4D Futurecraft line and claims to be using Carbon’s Digital Light Synthesis technology to mass produce the 3D printed footwear. New Balance has also been on a forward trend, beginning with the Zante Generate. They have collaborated with industry leaders like 3D Systems, HP, and Formlabs too—from launching the 3D printing platform, TripleCell, to presenting an obvious and impressive turn in their manufacturing techniques with the ability to customize shoes—and move away from the reliance on molds and direct printing.
Source: https://3dprint.com
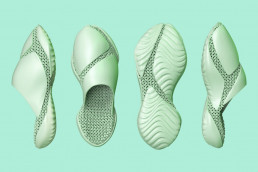
Lynxter 3D Printing Silicone onto Fabric with ViscoTec Printheads
German company ViscoTec develops systems needed for conveying, dosing, applying, filling, and emptying fluids, which includes printheads for viscous fluids and two-component 3D printing. Its innovations are used in many industries, from aerospace, e-mobility, and food to medical and pharmaceutical, and now textiles as well. French company Lynxter, which manufactures modular industrial machine tools and 3D printers, is using ViscoTec’s printheads for an interesting textile 3D printing project.
While 3D printing has been used before with textiles, the thermoplastics typically used in this application don’t have the elasticity, flexibility, texture, and wear resistance needed when you’re working with fabric. Lynxter sees 3D printing as a true production tool, and decided to take a closer look at how silicone 3D printing material behaves with textiles, since its modular S600D 3D printer can work with the soft, elastic material.
Silicone is a polymer with great chemical and UV ray resistance, which makes it good for fabricating medical prosthetics. But, the material also adheres well to fabric, a quality Lynxter is putting to good use in optimizing technical functions of textiles for its luxury goods and sportswear clients.
“3D printing of silicone makes it possible to meet the growing demand for product customization from consumers looking for uniqueness,” Lynxter wrote in an interview with ViscoTec. “This solution also gives the freedom to create patterns with complex 3-dimensional shapes or different layer heights, which are impossible to achieve with traditional processes. It offers greater possibilities for designing custom-made patterns, as well as a wide choice of positioning patterns on the fabric which were not always accessible with other processes. The user will be able to work more creatively, and the silicone’s characteristics ensure the expected comfort of a garment.”
Lynxter needed a compact printhead with limited mass and the ability to embed electrical components with standard AM control boards. It also had to be able to handle different compatible flow rates and viscosities. The tool head on Lynxter’s S600D printer can be easily changed in order to print different materials, which is why the company chose ViscoTec’s vipro-HEAD 3 for silicone printing, after testing it with several kinds of fabric, like polyesters and cottons, as well as standard and custom silicones, with multiple extrusion speeds, string width, and thicknesses. Lynxter also explained that the company’s accurate, reliable, and quality components made the choice a no-brainer.
The company selected a one-component RTV silicone, with a shore hardness of 34, to 3D print on the textile, as the “characteristics meet the constraints of use and maintenance of textiles: elasticity (high elongation rate), heat resistance, and resistance to moisture and chemicals.”
“Once the printing project has been defined, the machine deposits silicone beads on the fabric to create a 3D pattern. Printing and drying times will vary depending on the size and complexity of the project,” Lynxter wrote.
“We quickly and precisely create a 3-dimensional pattern on the fabric. The printing integrates perfectly with the type of textile, e.g. comfort, fluidity, elasticity. This ensures that the garment is pleasant to wear after the process. The aesthetic result is highly satisfactory. Following the various wear tests carried out, the silicone held well on the fabric when in use and showed good stability during washing.”
Lynxter says that 3D printing silicone on textiles can be considered “a real asset for companies,” as items can be fabricated in the actual area where products are made, which negates the use of go-between companies and shipping—creating a lower carbon footprint in the process. An additional benefit is an economic one, as this can lower “the margins linked to intermediaries and constitutes a gain in reaction time and efficiency for companies.”
Textiles with 3D printed silicone can be used in many applications requiring personalized and branded fabrics, such as furniture, fashion, sporting equipment, and others.
“Interesting projects will be further developed and implemented in the coming months,” Lynxter wrote. “We are still only just discovering the potential of this technology, but the feedback from the field is already very positive.”
Source: https://3dprint.com
Lynxter 3D Printing Silicone onto Fabric with ViscoTec Printheads
Chinese Designer’s 3D Printed Clothing Nominated for International Innovation Award
Typically held in London during the first weekend of June, this year’s Graduate Fashion Week (GFW) held by the Graduate Fashion Foundation had to be canceled due to the ongoing COVID-19 pandemic. Instead, the charitable organization found a new way to support initiatives from fashion graduates, as the organizers decided to introduce a new series of digital awards encompassing 22 categories – from childrenswear and fashion marketing to accessories and textiles – to make sure students still got a chance to promote their work.
Shortlisted for the Innovation Award in the Materials category was Xie Zimeng, from the Sichuan Fine Arts Institute in Chongqing, Western China. Her work leveraged 3D printing technology as she explored future trends in fashion in a semi-apocalyptic world consumed by plastic pollution, deforestation, and carbon emissions. In her presentation, titled Worship of Light and Shadow, the designer combined 3D printing and hollow projection light to form a circuit that illuminates a large area, instantly taking the viewer into Zimeng’s dark “cyberpunk” world. Particularly demonstrating how her creative design incorporates technology and light into a feminine silhouette that is both beautiful and elegant.
“My design concept is mainly based on the vision of the future world. In the future, people will cause an irreversible impact on the Earth due to various factors. In tens of thousands of assumptions, my design is aimed at the formation of the “polar night”, phenomenon due to environmental pollution in the future. At that time, people’s demand for light must go first,” said Zimeng to the Graduate Fashion Week Foundation. “In the future cyberpunk dark world, darkness makes people pay more attention to light and shadow, and gradually forms a unique aesthetic and demand for light and shadow.”
Like many before her, Zimeng’s focus to explore fashion outside of the limits of traditional textiles and craftsmanship led her to disruptive technologies. After creating her designs, she built a 3D model that was used to repeatedly test a light source in order to draw the figure that would eventually be hollowed out on the final printed model. The designer chose photosensitive resin material to 3D print the creation that went on to compete for the GFW award and then used an electric drill pen for hollowing out and polishing it. Followed by a coat of white matte and silver chrome spray paint to increase texture, and finally the installation of a LED light source and power controller to form a color slow flash effect.
Zimeng suggested that “in such a world, our demand for the role of clothing is not only to cover the body and keep warm; it is particularly important to let clothing itself become a light source that illuminates. The presentation of light and shadow on clothing has become a new aesthetic standard. In the way of expression, I chose the combination of 3D printing and hollow light to highlight the sense of future and technology.”
Inspired by cyber future designs of neon-lit cities that rely on everlasting technology to counter the effects of a permanent night sky, Zimeng created a bodysuit, complemented by a set of light-powered “wings” that irradiate color, as well as a protective neck covering and a leg holster. Once completed, the work was submitted to GFW and later showcased at the Chongqing Grand Art Market Blooming June Art Tour of the Sichuan Fine Arts Institute, at the Longfor ‘U’ City Paradise Walk in University City, China; as well as on the Chongqing Art Market’s newly launched Cloud Exhibition Hall, on the WeChat platform, which gives students the opportunity to display the entirety of their work.
During an interview with Upstream news, Zimeng said she was very interested in studying the future and functional direction of fashion, especially through 3D printing technology. Describing her creations as more of an accessory concept, she suggested that they may not be comfortable enough to wear yet, but she is already looking into the aesthetic needs of the future to make a few upgrades and improvements. Furthermore, as part of her particular vision, she outlines that her cyberpunk style has a sense of Avant-guard women soldiers living in a future society that struggles to survive in a slump while heavily relying on the rapid development of technology.
Designers have been using technological innovation to explore future trends in fashion and showcase their inspiration for years. 3D printing particularly has become a great tool for unconventional minds to create beyond the limits of traditional designs, moving away from the constraints of the industry and the standards of beauty in clothing, to make unique, daring, and powerful pieces. The need to express her vision led imaginative designer Zimeng to combine 3D printing with light to fabricate an eye-catching suit that makes a powerful statement about the future of our world. After all, at the forefront of her work is the environmental impact of our actions and the importance of taking care of Earth’s limited resources, to avoid her take on a futuristic sci-fi society living in “eternal night”.
Source: https://3dprint.com
Mikrotvornica - our new technology partner
Mikrotvornica has joined 3D-CPAM project! Learn more about them..
Mikrotvornica: Our passion for creating things is our fuel!
We are a team of creative enthusiasts, mechanical engineers and 3D printing specialists with a strong sense for aesthetics and functionality. This way we make superior products that bring joy to our clients faces and “conquer the market”.
In Mikrotvornica, we are growing a strong sense of purpose for all kinds of additive and digital manufacturing technologies! By combining them we made hundreds of high quality products and all kinds of BIG projects for our clients in Croatia and abroad. We are constantly using these skills to offer more to the community.
Our company has invented and implemented two special brands – Modax3D and 3DPrintaj platform in the course of only two years! Modax3D is inovative concept that makes a big difference in the field of industrial production. 3DPrintaj platform has educational purpose and brings value to the maker community!
Printing a test patch
PRINTING A TEST PATCH
This test print was a cooperation of Danit Peleg and Mikrotvornica coordinated by Institute Ruđer Bošković. Danit designed a pattern that is very similar to other patterns she uses when designing 3D printed clothes. This patch is dim. 32×10 cm.
Mikrotvornica used their large scale industrial printer to print this patch and, although it has capability to print with multiple bridges and heads, we used single-bridge, single-head print to get reference point for future improvements.
Printing time for this patch was 3.5 hours using TPU 98A filament and 4 hours using TPU 85A filament.
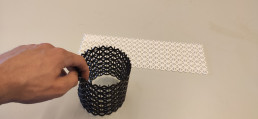
Meet(up) HPC: powering business growth event
Experts and practitioners from various EU countries, such as Ireland, Slovenia and Romania including member of our experiment team gave lecture about high-performance computing (HPC), how it can support them to save money and efforts through higher speed and why this becomes an indispensable resource in the digital age.